1. Test théorique et analyse
Des 3valves de pneusÉchantillons fournis par l'entreprise : deux vannes et une vanne non utilisée. Pour A et B, la vanne non utilisée est grisée. Figure 1 complète. La surface extérieure de la vanne A est peu profonde, celle de la vanne B est superficielle, celle de la vanne C est superficielle et celle de la vanne C est superficielle. Les vannes A et B sont recouvertes de produits de corrosion. Les vannes A et B sont fissurées au niveau des coudes, la partie extérieure du coude longe la vanne, l'embouchure de la bague de vanne B est fissurée vers l'extrémité, et la flèche blanche entre les surfaces fissurées sur la surface de la vanne A est indiquée. D'après ce qui précède, les fissures sont omniprésentes, les plus importantes et les plus répandues.
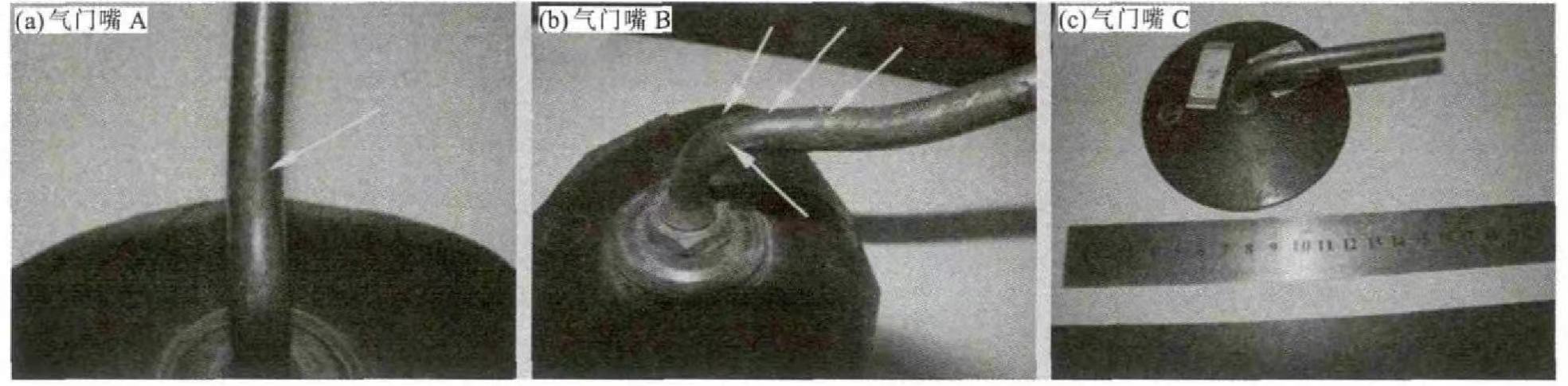
Une section de lavalve de pneuLes échantillons A, B et C ont été découpés dans le coude. La morphologie de la surface a été observée au microscope électronique à balayage ZEISS-SUPRA55 et la composition des micro-zones a été analysée par EDS. La figure 2 (a) montre la microstructure de la surface de la valve B. On observe la présence de nombreuses particules blanches et brillantes à la surface (indiquées par les flèches blanches sur la figure), et l'analyse EDS des particules blanches révèle une teneur élevée en S. Les résultats de l'analyse du spectre énergétique des particules blanches sont présentés à la figure 2 (b).
Les figures 2 (c) et (e) représentent les microstructures de surface de la vanne B. La figure 2 (c) montre que la surface est presque entièrement recouverte de produits de corrosion, et que les éléments corrosifs des produits de corrosion, selon l'analyse du spectre d'énergie, comprennent principalement S, Cl et O. La teneur en S dans certaines positions est plus élevée. Les résultats de l'analyse du spectre d'énergie sont présentés dans la figure 2 (d). La figure 2 (e) montre la présence de microfissures le long de la bague de vanne à la surface de la vanne A. Les figures 2 (f) et (g) représentent les micromorphologies de surface de la vanne C. La surface est également entièrement recouverte de produits de corrosion, et les éléments corrosifs comprennent également S, Cl et O, comme dans la figure 2 (e). La cause de la fissuration pourrait être une fissuration par corrosion sous contrainte (SCC) d'après l'analyse des produits de corrosion à la surface de la vanne. La figure 2(h) présente également la microstructure de surface de la valve C. On constate que la surface est relativement propre et que la composition chimique de la surface analysée par EDS est similaire à celle de l'alliage de cuivre, ce qui indique que la valve n'est pas corrodée. La comparaison de la morphologie microscopique et de la composition chimique des trois surfaces de valve montre la présence de milieux corrosifs tels que S, O et Cl dans le milieu environnant.
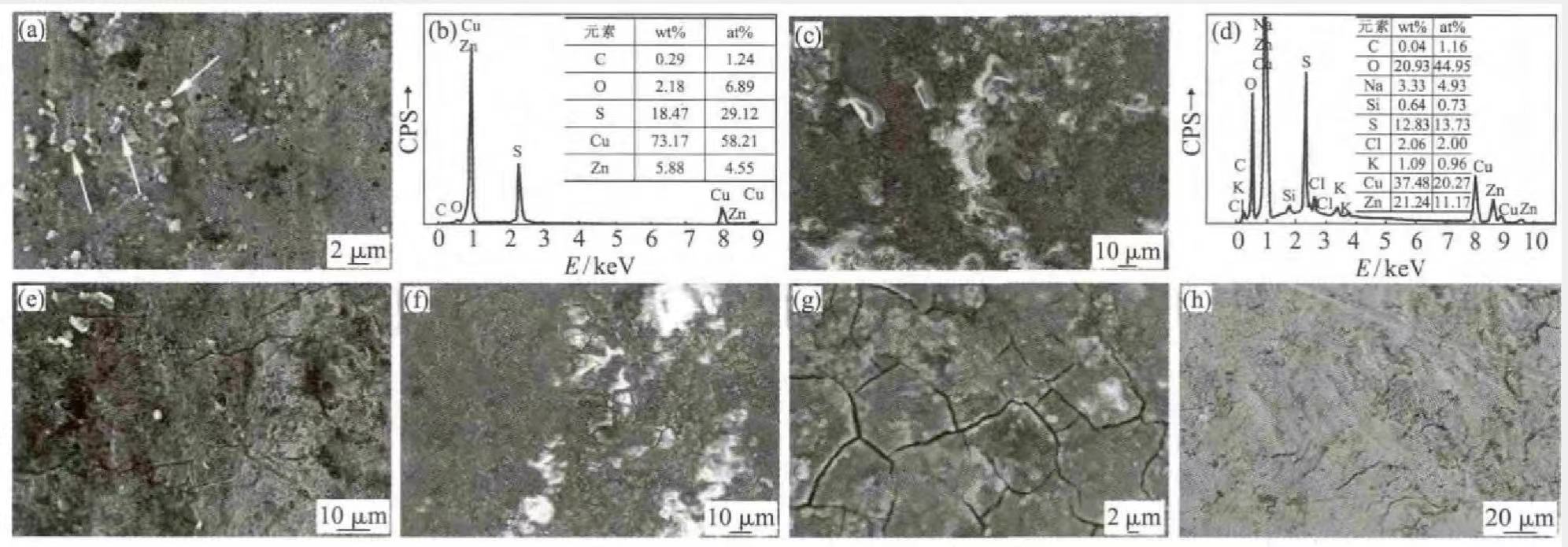
La fissure de la vanne B a été ouverte par un essai de flexion. Il a été constaté qu'elle ne pénétrait pas toute la section de la vanne, qu'elle se fissurait du côté de la courbure arrière et qu'elle ne se fissurait pas du côté opposé à cette courbure. L'inspection visuelle de la fracture montre une couleur foncée, indiquant une corrosion, et que certaines parties de la fracture sont foncées, ce qui indique une corrosion plus importante à ces endroits. La fracture de la vanne B a été observée au microscope électronique à balayage, comme le montre la figure 3. La figure 3 (a) montre l'aspect macroscopique de la fracture de la vanne B. On observe que la fracture externe près de la vanne a été recouverte de produits de corrosion, indiquant une fois de plus la présence de milieux corrosifs dans le milieu environnant. D'après l'analyse du spectre énergétique, les composants chimiques du produit de corrosion sont principalement S, Cl et O, et les teneurs en S et O sont relativement élevées, comme le montre la figure 3 (b). L'observation de la surface de fracture révèle une propagation de la fissure suivant le modèle cristallin. Un grand nombre de fissures secondaires sont également visibles en observant la fracture à fort grossissement, comme le montre la figure 3(c). Ces fissures sont indiquées par des flèches blanches. Les produits de corrosion et les schémas de croissance des fissures à la surface de la fracture illustrent à nouveau les caractéristiques de la fissuration par corrosion sous contrainte.
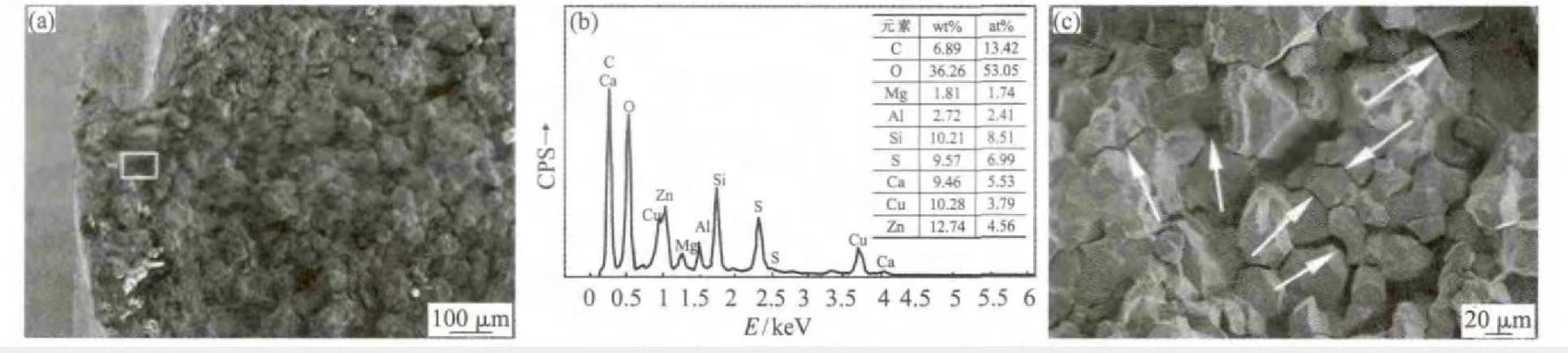
Français La fracture de la vanne A n'a pas été ouverte, retirez une section de la vanne (y compris la position fissurée), meulez et polissez la section axiale de la vanne et utilisez une solution de Fe Cl3 (5 g) + HCl (50 mL) + C2H5OH (100 mL) a été gravée, et la structure métallographique et la morphologie de la croissance des fissures ont été observées avec un microscope optique Zeiss Axio Observer A1m. La figure 4 (a) montre la structure métallographique de la vanne, qui est une structure biphasée α+β, et β est relativement fin et granulaire et distribué sur la matrice de phase α. Les schémas de propagation des fissures au niveau des fissures circonférentielles sont illustrés dans les figures 4(a), (b). Comme les surfaces de fissures sont remplies de produits de corrosion, l'espace entre les deux surfaces de fissures est large et il est difficile de distinguer les schémas de propagation des fissures. phénomène de bifurcation. Français De nombreuses fissures secondaires (marquées par des flèches blanches sur la figure) ont également été observées sur cette fissure primaire, voir Fig. 4(c), et ces fissures secondaires se propageaient le long du grain. L'échantillon de valve gravé a été observé par MEB, et il a été constaté qu'il y avait de nombreuses microfissures dans d'autres positions parallèles à la fissure principale. Ces microfissures provenaient de la surface et se sont étendues à l'intérieur de la valve. Les fissures présentaient une bifurcation et s'étendaient le long du grain, voir Figure 4 (c), (d). L'environnement et l'état de contrainte de ces microfissures sont presque les mêmes que ceux de la fissure principale, on peut donc en déduire que la forme de propagation de la fissure principale est également intergranulaire, ce qui est également confirmé par l'observation de la fracture de la valve B. Le phénomène de bifurcation de la fissure montre à nouveau les caractéristiques de la fissuration par corrosion sous contrainte de la valve.
2. Analyse et discussion
En résumé, on peut déduire que l'endommagement de la vanne est dû à une fissuration par corrosion sous contrainte due au SO2. La fissuration par corrosion sous contrainte doit généralement remplir trois conditions : (1) matériaux sensibles à la corrosion sous contrainte ; (2) milieu corrosif sensible aux alliages de cuivre ; (3) certaines conditions de contrainte.
Il est généralement admis que les métaux purs ne sont pas sujets à la corrosion sous contrainte, et tous les alliages y sont sensibles à des degrés divers. Pour les laitons, on considère généralement que la structure biphasée présente une sensibilité à la corrosion sous contrainte plus élevée que la structure monophasée. La littérature scientifique montre que lorsque la teneur en zinc du laiton dépasse 20 %, sa sensibilité à la corrosion sous contrainte est plus élevée, et plus cette teneur est élevée, plus elle est élevée. La structure métallographique de la buse à gaz, dans ce cas, est un alliage biphasé α+β, avec une teneur en zinc d'environ 35 %, dépassant largement les 20 %, ce qui lui confère une sensibilité élevée à la corrosion sous contrainte et répond aux conditions matérielles requises pour la fissuration par corrosion sous contrainte.
Pour les laitons, si aucun recuit de détente n'est effectué après déformation par écrouissage, une corrosion sous contrainte se produira dans des conditions de contrainte appropriées et en environnement corrosif. La contrainte à l'origine de la fissuration par corrosion sous contrainte est généralement une contrainte de traction locale, qui peut être une contrainte appliquée ou une contrainte résiduelle. Après le gonflage du pneu de camion, une contrainte de traction sera générée le long de l'axe de la buse d'air en raison de la pression élevée dans le pneu, ce qui provoquera des fissures circonférentielles dans la buse d'air. La contrainte de traction due à la pression interne du pneu peut être calculée simplement selon la formule σ=p·R/2t (où p est la pression interne du pneu, R le diamètre intérieur de la valve et t l'épaisseur de la paroi de la valve). Cependant, en général, la contrainte de traction générée par la pression interne du pneu n'est pas trop importante et l'effet de la contrainte résiduelle doit être pris en compte. Les positions de fissuration des buses de gaz se situent toutes au niveau du coude arrière, et il est évident que la déformation résiduelle au niveau du coude arrière est importante et qu'il existe une contrainte de traction résiduelle à cet endroit. En fait, dans de nombreux composants en alliage de cuivre, la fissuration par corrosion sous contrainte est rarement causée par des contraintes de conception, et la plupart d'entre elles sont dues à des contraintes résiduelles invisibles et ignorées. Dans ce cas, au niveau du coude arrière de la valve, la direction de la contrainte de traction générée par la pression interne du pneu est cohérente avec la direction de la contrainte résiduelle, et la superposition de ces deux contraintes fournit la condition de contrainte pour la fissuration par corrosion sous contrainte.
3. Conclusion et suggestions
Conclusion:
La fissuration de lavalve de pneuest principalement causée par la fissuration par corrosion sous contrainte causée par le SO2.
Suggestion
(1) Tracer la source du milieu corrosif dans l'environnement autour duvalve de pneu, et évitez tout contact direct avec le milieu corrosif environnant. Par exemple, une couche de revêtement anticorrosion peut être appliquée sur la surface de la vanne.
(2) La contrainte de traction résiduelle du travail à froid peut être éliminée par des procédés appropriés, tels que le recuit de détente après pliage.
Date de publication : 23 septembre 2022